Step 1
Mixing, churning, kneading and kneaded blocks of incense paste
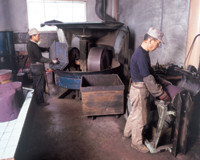
After the materials are measured and mixed for a given brand of incense, the mixture is loaded into a vat and then churned. Temperature and humidity are carefully regulated throughout this process. Dyes and water are added and the mixture is thoroughly kneaded into a uniform incense paste. The kneaded incense paste is then molded into cylinder shaped blocks about 30 cm in diameter called neri-tama.
Step 2 Extrusion, cutting and straightening
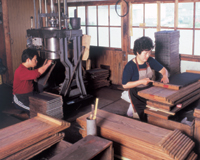
The blocks of kneaded incense paste are inserted into an extruder (oshi-dashi-ki) to form cylinder shaped strands through the metal holes (sugane) much like strands of pasta ate made. The strands ate placed on the receiving tray (bon-ita) and then cut free from the extruder with a bamboo spatula (take-bera).The strands are then laid side by side (no gaps) on drying boards (hoshi-ita), cut to the proper length and then straightened.
Step 3 Drying
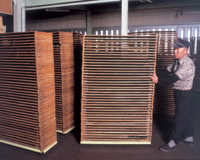
The drying boards are then moved to the drying area where the strands can dry naturally by exposure to Awaji Island's west wind. Drying takes about three to five days.
Step 4 Bundling and packaging
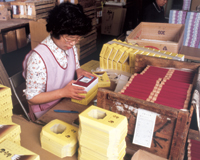
Once the strands ate dried, they undergo rigorous inspection, are bundled and then packaged in containers.
Finish
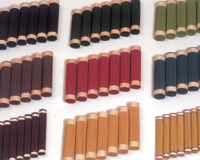
* Many parts of the methods above are now automated and have been replaced by modern methods.